
- #Ishikawa diagram categories how to#
- #Ishikawa diagram categories software#
- #Ishikawa diagram categories series#
- #Ishikawa diagram categories free#
#Ishikawa diagram categories software#
Use the generic categories but adapt them to your process: service representative, service order, software systems, reference manuals, and access. Here you may be able to identify critical supply. People, process, machines, materials, and measurement are the major causes.Įach step of the process is a major cause. 4S Fishbone diagram: The categories in a 4S Fishbone diagram are surroundings, suppliers, skills, and systems. What is a Fishbone Diagram (aka Cause & Effect Diagram) Man/Mind Power (People) Method (Process) Machines (Program) Materials (Product) Measurements (.
#Ishikawa diagram categories series#
A series of smaller "bones" coming off the main bones to show the " Five Whys" used to identify the cause-effects.The head of the fish ( problem statement).An Ishikawa or fishbone diagram always contains: The different causes originating a Problem have been traditionally classified into 6 different Activities: Material. It is known as the Fishbone Diagram because of its resemblance to a Fishbone. You can analyze root causes using the classic format, step-by-step format, or a custom format. The Ishikawa Fishbone is a Cause-Effect Diagram that helps to find the Root causes of any type of Problem. There are many ways to use the Ishikawa diagram. Here is how you can create an Ishikawa fishbone diagram in four easy steps.

The ribs represent the causes of an event, and the skeleton's head indicates the outcome.

This is because Ishikawa diagrams look like a fish skeleton.
#Ishikawa diagram categories free#
Free Agile Lean Six Sigma Trainer Trainingįishbone Diagram » Types of Fishbone Diagrams Ishikawa Fishbone Diagram Types Ishikawa diagrams are sometimes referred to as fishbone diagrams, Fishikawa, herringbone diagrams, or cause and effect diagrams.Animated Lean Six Sigma Video Tutorials.This quality Ishikawa diagram (cause and effect diagram) template is included in the Fishbone Diagram solution from the Management area of ConceptDraw Solution Park. The basic concept was first used in the 1920s, and is considered one of the seven basic tools of quality control." Ishikawa diagrams were popularized by Kaoru Ishikawa in the 1960s, who pioneered quality management processes in the Kawasaki shipyards, and in the process became one of the founding fathers of modern management. (6) Environment: The conditions, such as location, time, temperature, and culture in which the process operates. (5) Measurements: Data generated from the process that are used to evaluate its quality The six categories are Procedures, Policies, Place, Product, People, and Processes. (4) Materials: Raw materials, parts, pens, paper, etc. What are the 6 Categories of Fishbone Diagrams. (3) Machines: Any equipment, computers, tools, etc. (2) Methods: How the process is performed and the specific requirements for doing it, such as policies, procedures, rules, regulations and laws (1) People: Anyone involved with the process It is known as the Fishbone Diagram because of its resemblance to a Fishbone. One of the first steps in creating a fishbone diagram is determining the factors that contribute to variations within a process. Causes are usually grouped into major categories to identify these sources of variation. The Ishikawa Fishbone is a Cause-Effect Diagram that helps to find the Root causes of any type of Problem.
#Ishikawa diagram categories how to#
This article explains how to make one with the Six Sigma package in R. Each cause or reason for imperfection is a source of variation. Quality Nugget: Creating Ishikawa (Fishbone) Diagrams With R ( Software Quality Professional) A fishbone diagram connects causal links in major categories with an outcome, or effect. "Common uses of the Ishikawa diagram are product design and quality defect prevention, to identify potential factors causing an overall effect. This Ishikawa diagram (cause and effect diagram) template is included in the Fishbone Diagram solution from the Management area of ConceptDraw Solution Park. (The "5" in the name derives from an empirical observation on the number of iterations typically required to resolve the problem.)" Here are a few more you may find helpful. It covers all the major aspects we come across in a manufacturing setting.
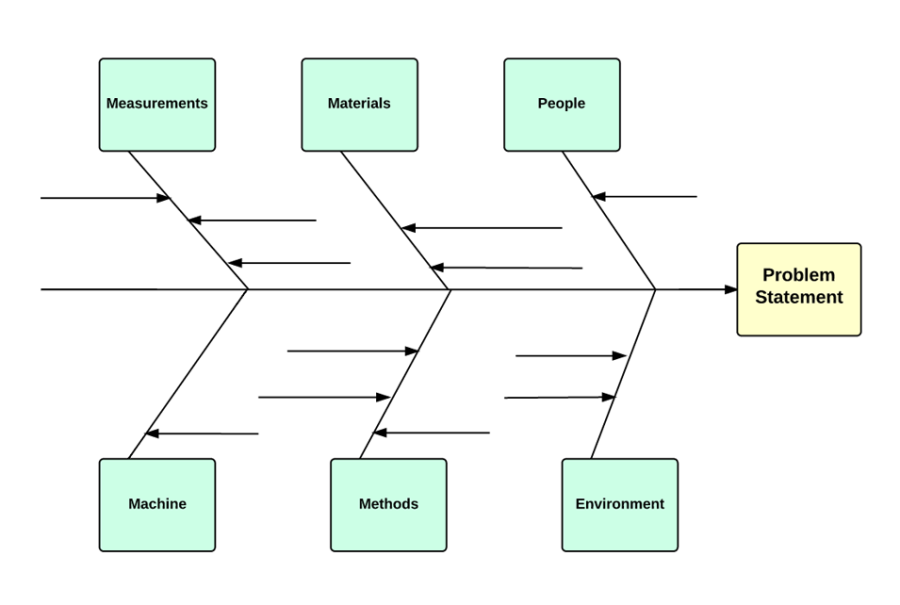
The primary goal of the technique is to determine the root cause of a defect or problem. 5M/1E (Standard Manufacturing) Fishbone Diagram Most of the time, manufacturing teams will use these six categories in their Fishbone Diagrams: Machine, Methods, Measurements, Materials, Manpower, and Environment. "The 5 Whys is an iterative question-asking technique used to explore the cause-and-effect relationships underlying a particular problem. Causes can be traced back to root causes with the 5 Whys technique." Learn about the other 7 Basic Quality Tools at. They will typically be one of the traditional categories mentioned above but may be something unique to the application in a specific case. The Fishbone Diagram, also known as an Ishikawa diagram, identifies possible causes for an effect or problem. These groups can then be labeled as categories of the fishbone. "Cause-and-effect diagrams can reveal key relationships among various variables, and the possible causes provide additional insight into process behavior.Ĭauses can be derived from brainstorming sessions.
